How does the machining center work?
The Ding principle of the machining center is to formulate the process plan according to the parts drawing, and automatically process the part processing program by hand or computer, and change the various machine action and all process parameters required by the part into the information code acceptable to the numerical control device of the machine tool. The code is stored on an information carrier (punctured tape, disk, etc.) and the information carrier is sent to the input device. Read the information and send it to the numerical control device, or use the computer and the machining center to communicate directly to realize the input and output of the part program.
The information entering the numerical control device is converted into a pulse signal through a series of processing and calculation. Some signals are sent to the servo system of the machine tool, converted and amplified by the servo mechanism, and then passed through the transmission mechanism. Driving machine-related components allows the tool and workpiece to strictly perform the corresponding motions specified by the part program. Additional signals are sent to the programmable controller for sequential control of other auxiliary actions of the machine to automatically change the tool.
The basic composition of the machining center:
The composition of the machining center varies depending on the type, function, and parameters of the random bed. The machine itself is divided into basic components and selected components. The CNC system has basic functions and optional functions. The machine parameters have main parameters and other parameters. Machine tool manufacturers can produce according to the requirements put forward by users, but the basic functions and component compositions of similar machine tools generally have little difference. Although various types of machining centers have appeared, their shapes and structures are different, but in general they are mainly composed of the following major parts.
1) Basic part: consists of the bed, column, beam, workbench and base. They mainly bear the static load of the machining center and the cutting load generated during machining, and support and guide the various parts of the machining center. Therefore, the basic support member must have sufficient rigidity, high natural frequency and large damping. These workpieces are usually cast iron or welded steel structural parts, which are the largest volume and weight of the basic components in the machining center.
2) Spindle components: It consists of the spindle head, the spindle motor, the spindle and the spindle bearing. The start, stop and shift of the spindle are controlled by the numerical control system, and the cutting motion is carried out by the cutter mounted on the spindle, which is the power output component of the cutting process. The main shaft system is the main component of the machining center. Compared with the conventional machine tool spindle system, the Jiading central spindle system has higher rotation speed, higher rotation precision and higher structural rigidity and vibration resistance.
3) Feed mechanism: consists of feed servo motor, mechanical transmission and displacement measuring components. It drives a moving part such as a workbench to form a feed motion. The feeding center of the machining center directly realizes the feeding and positioning of the linear or rotary motion, which has a great influence on the precision and quality of the machining. Therefore, the requirements for the feeding system of the center are the motion precision, the motion stability and the quick response capability. .
4) CNC system (CNC): The CNC part of the machining center consists of CNC device, programmable controller, servo drive and operation panel. It is the control center for the machining process. The CNC system generally consists of a central processing unit, a memory, and an input and output interface. The central processing unit is composed of a mountain memory, an arithmetic unit, a controller, and a bus. The main feature of the CNC system is that the storage of the person in charge, the processing of data, the interpolation operation, and the various control functions of the machine tool are all completed by computer software, which can increase the functions that are difficult to realize by the many logic circuits. The computer and other devices can be connected through an interface device. When the control object changes, just change the software and interface.
5) Automatic Tool Changer (ATC): Automatic Tool Changer (ATC) consists of components such as tool magazine, robot and drive mechanism. The magazine is the device for storing all the tools used in the machining process; the magazine has a disc. Drum and chain and other forms, from a few to a few hundred. When the tool needs to be changed, according to the CNC system command, the robot is extended (or by other means) to remove the tool from the magazine into the spindle. The structure of the manipulator is different from the relative position and structure of the main shaft, such as single arm type, double arm type, rotary type and orbit type. Some machining centers use the movement of the earthen box or the magazine to realize the tool change without using a robot. Although the tool change process, the tool selection method, the tool bank structure, the robot type, etc. are all different, but under the control of the numerical control device and the programmable controller, the motor and the hydraulic or pneumatic mechanism drive the tool magazine and the robot to realize the tool. Choice and exchange. Mounting the contact sensor Oe in the mechanism also enables measurement of tool and workpiece errors.
6) Auxiliary devices: including lubrication, cooling, chip evacuation, protection, hydraulic, pneumatic and detection systems. These devices, although not directly involved in the cutting motion, play a role in the heating efficiency, machining accuracy and reliability of the center. The role of security is therefore an indispensable part of the center of Gading. Due to the high production efficiency of the machining center, the well can be automated for a long time, so the problems of cooling, lubrication and chip removal are more prominent than conventional machine tools. Large cutting capacity requires strong cooling and timely chip removal. A large amount of cooling and lubricating fluids also puts higher demands on the sealing and leakage of the system. Thereby promoting the production of semi-closed, fully enclosed machine tools.
7) Automatic pallet change system: Some machining centers are equipped with two automatic exchange workpiece pallets for further shortening non-cutting time: one is installed on the workbench for processing, and the other is located outside the workbench for loading and unloading workpieces. When the workpiece on a pallet is finished, the pallets are automatically exchanged for new parts processing, which reduces auxiliary time and improves machining efficiency.
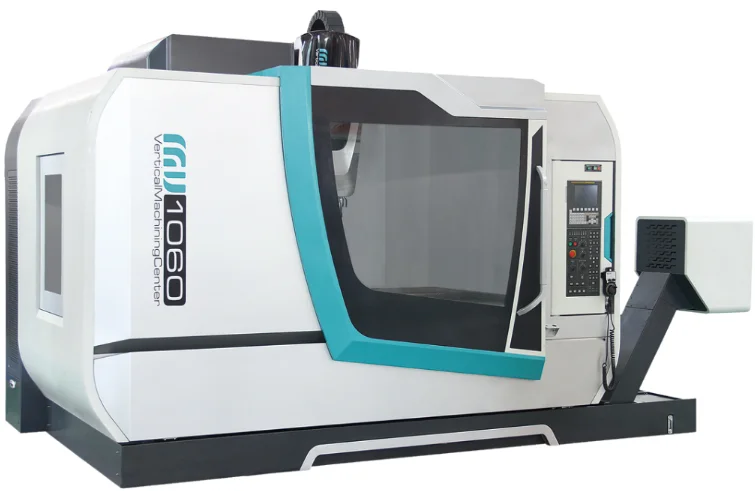
Mainly used in medium-sized parts and molds, the workpiece in a fixture may be for the completion of milling, drilling, boring, rearing and other process of processing, it can be single used and can also be used for multiple opeartions on parts in a production lile. Cutting with powerful, high-speed positioning mechanical and electric intergration, automatic chip control and security protection features.
MV series universal CNC vertical machining center is mainly used for the processing of medium-sized parts and molds. After a workpiece is clamped, the workpiece can be continuously processed by milling, drilling, boring, and reaming. It can be used on a single table or on multiple lines. With powerful cutting, to tell the location, mechanical and electrical integration, automatic chip removal, safety protection and easy operation and so on.
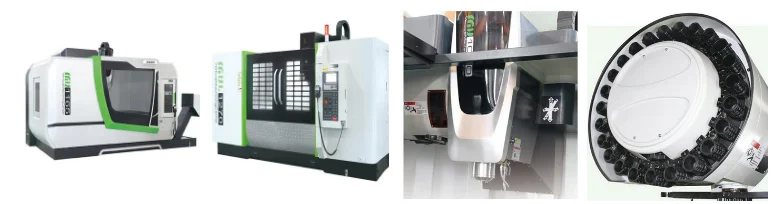